ANNOUNCEMENT: E-PLUS 3D Direct to Metal Printing and Osseo Group Join Forces
- Stuart Anderton
- Jun 5, 2024
- 5 min read
Updated: Jul 1, 2024
We are thrilled to announce our latest collaboration with 3-Plus 3D, bringing you the state-of-the-art EPM-150 Metal Printer. This direct to metal printing technology is now available from Osseo Group, set to transform the landscape of dental manufacturing.
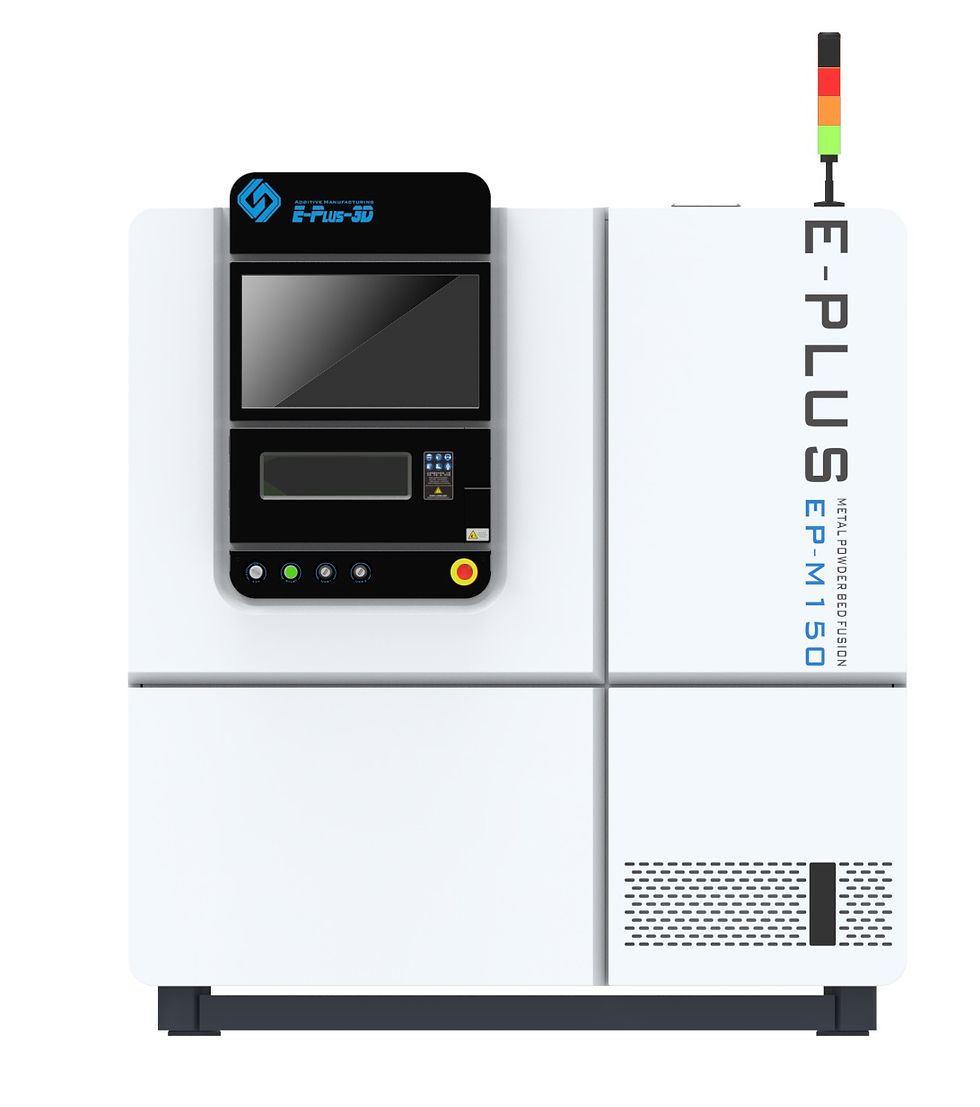
Introducing the EPM-150 Metal Printer
The EPM-150 Metal Printer, designed by 3-Plus 3D , is specifically tailored for dental applications. This advanced printer combines precision, reliability, and versatility, making it an invaluable tool for dental technicians and laboratories.
Key Features of the EPM-150 Metal Printer:
High Precision Printing: Utilising cutting-edge laser technology, the EPM-150 ensures exceptional detail and accuracy, critical for creating precise dental components.
Durable and Reliable: Engineered for consistent performance, this printer provides long-term reliability, making it a robust addition to any dental lab.
Material Flexibility: Capable of printing with various metal powders, the EPM-150 supports a wide range of dental applications, from crowns and bridges to custom implants.
How Direct to Metal Printing Works
Direct to metal printing, also known as metal additive manufacturing, involves a sophisticated electrooptical process where a high-powered fibre laser fuses metal powder layer by layer to build a component. Here's a detailed breakdown of the process:
The process begins with a digital model of the dental component created using CAD software. The design is then uploaded to the printer's software.
Inside the printer, a thin layer of metal powder (titanium or cobalt chrome) is spread evenly across the build platform using a recoating roller. This forms the initial layer for the printing process.
Layer Solidification:
Border: The fibre laser first traces the outer boundary of the layer, ensuring precise edges and defining the shape of the component.
Raster Hatching: The laser then fills in the interior of the layer with a raster pattern, systematically fusing the powder. This technique ensures a solid and dense build.
Once the layer is complete, the build platform lowers by a predefined layer thickness (usually a few microns), ready for the next layer of powder to be spread.
This cycle of powder spreading, laser scanning, and platform lowering is repeated layer by layer. The precision of the laser and the controlled environment within the printer ensure each layer adheres perfectly to the previous one, building up the component.
This method offers unparalleled precision and customisation, allowing for the creation of complex and detailed structures directly from digital designs without fear of miscasts, thermal or hygroscopic expansion and distortions.

Benefits of Direct to Metal Printing
Direct to metal printing offers numerous advantages over traditional manufacturing methods:
Faster Production Times: Digital design to final product, reducing lead times significantly.
Cost Efficiency: Streamlined processes reduce production costs by eliminating multiple intermediate steps.
Customisation: Each print can be customised to meet the specific needs of individual patients, ensuring a perfect fit and optimal functionality.
Comparison with Traditional Techniques
Manual Lost Wax Technique:
Create Wax Model: A wax model of the dental component is manually crafted.
Investing: The wax model is encased in a ceramic mould material.
Burnout: The wax is melted away in a furnace, leaving a cavity in the shape of the component.
Casting: Molten metal is poured into the cavity to form the component.
Cooling and Removal: The metal is allowed to cool and solidify before the ceramic mould is broken away to reveal the final part.
Finishing: The metal part is cleaned and polished to the desired finish.
Printed Lost Wax Technique:
Design: A digital model of the component is created using CAD software.
3D Printing Wax Model: The digital model is 3D printed in wax.
Investing: The printed wax model is encased in a ceramic mould material.
Burnout: The wax is melted away in a furnace, leaving a cavity in the shape of the component.
Casting: Molten metal is poured into the cavity to form the component.
Cooling and Removal: The metal is allowed to cool and solidify before the ceramic mould is broken away to reveal the final part.
Finishing: The metal part is cleaned and polished to the desired finish.
Direct to Metal Printing:
Design: A digital model of the component is created using CAD software.
3D Printing: The digital model is directly printed in metal by fusing metal powder layer by layer using a high-powered laser.
Post-Processing: The printed metal component is cleaned and may undergo additional treatments like heat treatment or surface finishing.
Labour Efficiency
One of the significant advantages of direct to metal printing is the reduction in manual labour required. Traditional techniques like the manual lost wax method involve intensive handcrafting and multiple stages of manual intervention, which can be time-consuming and prone to human error. Even with the printed lost wax technique, there are still several manual steps involved in the process. In contrast, direct to metal printing automates much of the production process, from digital design to final product, reducing the need for skilled manual labour and allowing technicians to focus on other critical tasks. This not only enhances productivity but also ensures a higher level of consistency and precision in the final product.
Energy Consumption Comparison
Direct to metal printing is significantly more energy-efficient compared to traditional methods. The manual lost wax technique and printed lost wax technique both require multiple stages of heating and cooling, which consume substantial amounts of energy. In contrast, direct to metal printing utilises a precise laser system that reduces overall energy consumption by streamlining the process and minimising waste.
Our Commitment to Innovation
Our collaboration with E-PLUS 3D highlights our dedication to staying at the forefront of technological advancements in dental manufacturing. The addition of the EPM-150 Metal Printer to our product lineup underscores our commitment to providing cutting-edge tools and services for dental technicians and laboratories.
About the EPM-150 Metal Printer
The EPM-150 Metal Printer is designed to integrate seamlessly into dental workflows. It features a user-friendly interface and robust software support, ensuring smooth and efficient operations in dental labs. The EPlus 3D EP-M150 utilises a fibre laser(s) to directly melt elemental or alloy metal powders, crafting dental restorations such as crowns, bridges, and partials. Renowned for its swift production, cost-effectiveness, and superior quality, the EP-M150 stands as the premier choice for dental practitioners worldwide. Printing a full plate of teeth (approximately 220 crowns) takes about 5.5 hours– a plate of partials (around 15 pieces) takes approximately 6.5 hours.
With a simple "One-click printing" feature, operating the EP-M150 is incredibly straightforward. The EP-M150 boasts low operational costs thanks to its improved powder feeding and sieving system, achieving a remarkable material utilisation rate of approximately 550 crowns printed from just 1kg of powder.
The self-developed electrooptical system and high-precision parallax correction algorithms guarantee impeccable printing quality, capturing even the finest details with precision regardless of the parts position on the plate.
What's the specs?
Machine Model - EP-M150
Build Chamber (XxYxZ) - Φ 153mmx80mm³
Optical System - Fiber Laser, 200W
Spot Size - 40-60μm
Max Scan Speed - 8m/s
Build Speed
Single laser: 5~20cm³/h
Dual laser: 8~35cm³/h
Layer Thickness - 20μm -50μm
Power Supply - 220V, 2.5KW, 11A, 50~60Hz (Dual laser: 3.5KW, 20A)
Gas Supply - Ar/N2
Oxygen Content - ≤100 ppm
Dimension (WxDxH) - 1750x810x2190mm³
Weight - 900kg
Software - EP Control, EPHatch
Input Data Format - STL
What's included in the package
Data preparation software
Electrical work, installation and onsite training
Vacuum drying oven for alloy powder
Industrial vacuum cleaner for alloy powder recovery
Bandsaw for removal of printed parts
Post-production annealing furnace for recrystallising parts
Get Started with Osseo Group
We invite all dental technicians and laboratories to explore the benefits of our new direct to metal printers. Whether you're looking to enhance the quality of your dental restorations or reduce production times, headcount and overheads, the EPM-150 Metal Printer from Osseo Group is the solution you need.
Click HERE to read the full specs and a what's included or give our office a call at 1300 029 383 to speak with a production specialist or sales.